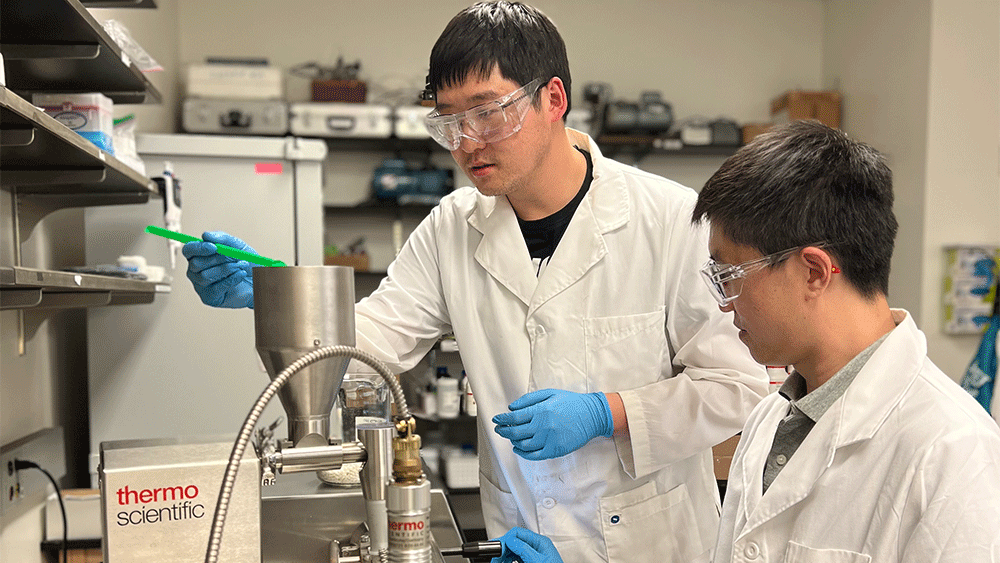
Manufacturing Metal-Organic Framework-Based Composites for Efficiency: Dr. Qingsheng Wang, associate professor and George Armistead ‘23 Faculty Fellow in the Artie McFerrin Department of Chemical Engineering at Texas A&M University, and his team of researchers have spent over three years finding more efficient ways to manufacture metal-organic framework (MOF)-based composites for industrial applications such as flame retardants.
MOFs are a class of crystalline materials with permanent porosity and wide applications, including gas purification, gas separation, water remediation, catalysis and drug delivery. However, process improvement is required to produce MOFs at a higher capacity in industry as the use and applications of MOF-based composites expand.
“To produce MOFs requires a deep understanding of process engineering, stringent conditions, and even with that, only a small amount can be produced at a time,” said Wang. “Many alterations are needed to improve the process if we want to mass-produce MOFs.”
Wang’s group published four studies in ACS Publications regarding their discoveries on MOF stability, MOF development processes, manufacturing MOF-based composites and their applications in flame retardancy.
Currently, most MOF-polymer composites are prepared by a discretely bottom-up principle that requires complex chemical reactions blended within different polymers in solutions. This multistep process entails significant time, energy and money to produce minimal quantities.
By combining parts of the MOF’s development process, Wang’s team has discovered a one-step method using reaction extrusion to produce MOF-based composites on a larger scale safely and effectively. Together with the heating condition, applied shear and compressive forces, MOFs can meet the required reaction conditions for mechanochemical synthesis.
In addition, the findings provide new insights into creating MOF-based polymer systems for polyolefins, reducing their smoke emissions and enhancing flame retardancy during combustion. The method also improved safety and efficiency by enhancing the thermal stability and mechanical properties of the MOF while decreasing its flammability.
This work was recently published in ACS Sustainable Chemistry & Engineering.
“If we use reactive extrusion manufacturing, we can take the starting material combined with a polymer to produce MOFs and directly mix it with plastics by neglecting several reaction steps in conventional hydrothermal methods,” said Wang. “Using this process, each day we can get around kilogram scale compared to the traditional method, which usually can produce only in gram scale.”
They hope to see this method used in industry for progressing sustainability efforts, process improvement and process safety.
In their study published in Industrial & Engineering Chemistry Research, Wang showed the use of MOF as a flame retardant. A commercially available MOF was incorporated into an intumescent flame retardant/polypropylene (IFR/PP) composite system. The results show that the additives exhibit a strong synergistic effect between them for improvement of the formation and stability of the intumescent char layer to prevent the intensive burning of PP.
These findings could improve IFR systems for polyolefins, reducing their smoke emissions during combustion. Considering that all the raw materials are commercially available, and the preparation method is compatible with current industrial processes, the methodology presented in this study can be expanded for industrial applications.
“We can use MOFs in so many ways — from water treatment to carbon capture,” Wang said. “I would like to continue improving this process so that industry can use MOFs on a larger scale in various useful applications.”
Manufacturing Metal-Organic Framework-Based Composites for Efficiency: Original Article
Metal-organic frameworks cut energy consumption of petrochemicals